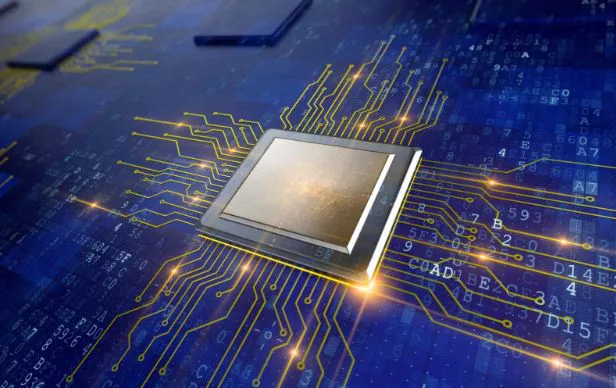
Semiconductor manufacturing is experiencing rapid and dynamic growth. The exponential evolution is making it one of the most swiftly evolving industries globally. As technology is advancing, the electronic devices are progressively shrinking in size.
Behind this constant innovation lies the incredible field of “computational lithography”.
It is the heart of semiconductor industry. After all, it blends the power of computers, mathematics, and precision engineering. Only to create intricate microscale structures on silicon wafers.
It holds the key to unlocking the next generation of electronic devices. Thus, propelling us into a future where technology transcends its current limits.
In the world of computational lithography, as the demands for greater complexity and miniaturization have grown, two techniques have emerged as game-changers:
- Inverse Lithography Technology (ILT)
- Source Mask Optimization (SMO)
Inverse Lithography Technology (ILT)
As the name suggests, the technique “inverses” the traditional lithography process. Conventionally, a predefined design was photo-masked onto a silicon wafer. While, ILT gave creative wings to designers. It enabled etching of the pattern on the wafter itself. The ILT algorithm calculates the optimal mask pattern that will produce the desired wafer pattern.
By taking the advantage of the computational resources and optimization algorithms, ILT has become an indispensable technique for not only pattern transfer but also in enhancing the resolution. Consequently, the remarkable tech has enabled the production of increasingly complex and advanced semiconductor devices.
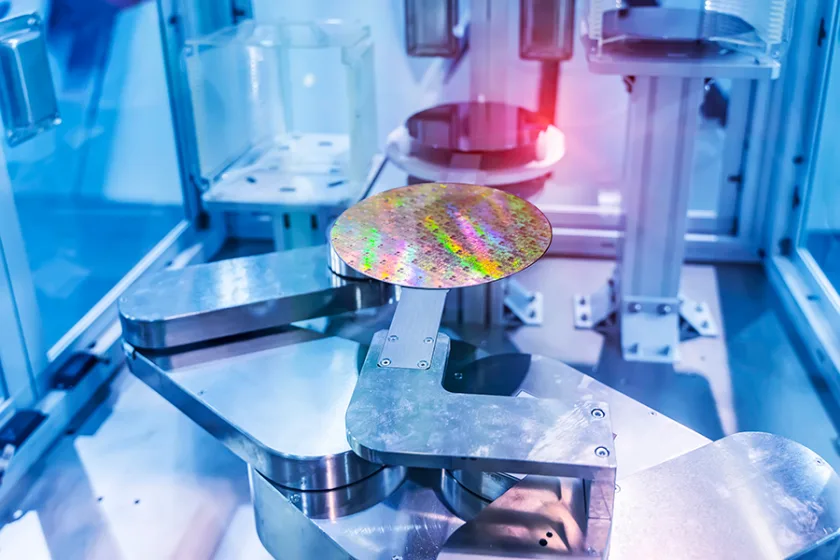
ILT is a master artist
In the world of semiconductor manufacturing, ILT is considered as a master artist, that creates masterpiece on the canvas of a silicon wafer.
When it comes to important variables, there are two key players that set the stage for Inverse Lithography Technology (ILT):
- the initial mask pattern and
- the target pattern on the wafer.
Although, the process starts with initial mask pattern but ILT continuously tweaks and adjusts it until there is minimum or no differences between the desired and actual patterns.
After all, it is a dance of optimization, where ILT strives for nothing less than perfection. Just as a dancer seeks to captivate the audience with its flawless performance, ILT aims to captivate the world of lithography with its impeccable results.
Source Mask Optimization (SMO)
Source Mask Optimization (SMO) is a remarkable advancement that takes computational lithography to new heights.
While Inverse Lithography Technology (ILT) focuses on refining the mask pattern, SMO goes a step further by simultaneously optimizing both the source illumination and the photomask pattern.
Source illumination: The source illumination refers to the light source, which is used in the lithographic process. For instance, it could be either advanced laser or other light-emitting technology.
The various characteristics of the source illumination significantly affect the pattern that is formed on the wafer. The features include, intensity, shape, polarization, and spectral content.
Photomask pattern: It is a transparent plate or template that contains the pattern to be transferred onto the wafer. It is also called as the reticle.
It acts like a stencil through which light passes to create the desired pattern on the silicon wafer during the lithographic process.
SMO algorithms look for possibilities in design space of source and mask patterns to bring about the best lithographic performance. The process takes the following variables into account:
- shape, intensity, and coherence properties of the illumination source, and
- optimization of the corresponding mask pattern, to improve resolution and depth of focus.

Takeaway
When it comes to cutting-edge devices with smaller feature sizes, higher densities, and increased performance, ILT and SMO have emerged as indispensable techniques in the field of computational lithography.
If we look ahead, the integration of ILT and SMO with machine learning and artificial intelligence holds great promise.
By leveraging the power of data-driven models, these techniques can autonomously enhance their optimization capabilities. And consequently, augment the futuristic lithographic performances.